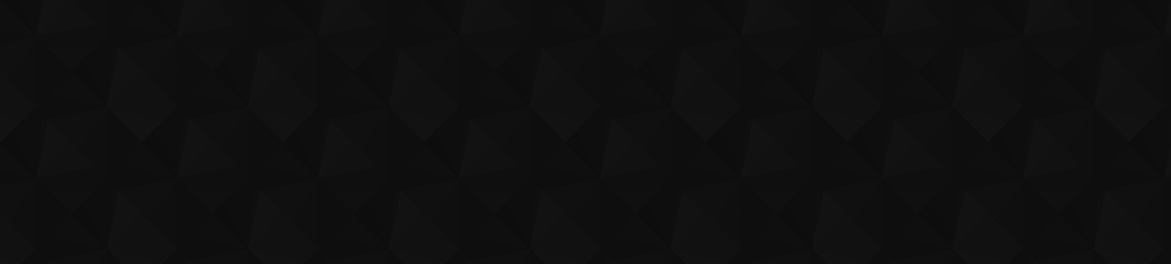
- 135
- 1 165 818
routercnc
Приєднався 29 жов 2016
Ep01: Plasma CNC intro | Bestarc BTC500XP 11th Generation
Here we go again on another CNC project. This time with a plasma cutter.
I've been wanting to do this for a long time, and was one of the reasons for buying my air compressor. I have no prior experience with plasma cutting, but have plenty of experience with CNC machines. So hopefully we can get this to work!
In this video I give a quick introduction to the plasma cutter, and give an overview of my CNC plans. Enjoy!
I've been wanting to do this for a long time, and was one of the reasons for buying my air compressor. I have no prior experience with plasma cutting, but have plenty of experience with CNC machines. So hopefully we can get this to work!
In this video I give a quick introduction to the plasma cutter, and give an overview of my CNC plans. Enjoy!
Переглядів: 1 523
Відео
Hyundai 50L air compressor: 2 year review with noise measurements
Переглядів 719Місяць тому
In this video we revisit the Hyundai air compressor I bought (with my own money) 2 years ago. What do I like, and what do I not like? Also, time to test just how quiet this thing is by comparing it to other familiar workshop tools. To help me out Banggood kindly sent me a Sound Level Meter to review (free of charge, but they had no influence over the video content or script). Link to purchase t...
Ep55: Drill Press upgrade | Finished at last!
Переглядів 1,6 тис.2 місяці тому
It's been a long time coming but this project is finally finished! I'll use it for a while and see if there are any other 'adjustments' needed. I've enjoyed the journey, now time to move onto something else. If you want to see how I got to this point in the build check out this link to the playlist: ua-cam.com/video/NiXFlVzR29Y/v-deo.html And for the CNC machine build (short version) check out ...
Ep54: Drill Press upgrade | Software!
Переглядів 1,8 тис.2 місяці тому
Time to write some new software to improve the functionality, hurrah :) Also, discovered new hardware issue(s), boo :( If you want to see how I got to this point in the build check out this link to the playlist: ua-cam.com/video/NiXFlVzR29Y/v-deo.html And for the CNC machine build (short version) check out this playlist: ua-cam.com/play/PLBhXglGlotqwcu7XSOL7SebFkrHVn7Plx.html Link to my long bu...
Ep53: Drill Press upgrade | Enclosure FINISHED!
Переглядів 2,3 тис.3 місяці тому
The main enclosure for the knee is now finished and working! If you want to see how I got to this point in the build check out this link to the playlist: ua-cam.com/video/NiXFlVzR29Y/v-deo.html And for the CNC machine build (short version) check out this playlist: ua-cam.com/play/PLBhXglGlotqwcu7XSOL7SebFkrHVn7Plx.html All music is free to use from the UA-cam audio library for creators
Ep52: Drill Press upgrade | Progress on the enclosure
Переглядів 1,3 тис.3 місяці тому
Almost, almost done on the enclosure so I thought I would share the latest updates. Link to 'My Tech Fun' channel showing a comparison of 3D printed material creep resistance: ua-cam.com/video/88pk2cNOeGE/v-deo.html If you want to see how I got to this point in the build check out this link to the playlist: ua-cam.com/video/NiXFlVzR29Y/v-deo.html And for the CNC machine build (short version) ch...
Ep51: Drill Press upgrade | Starting the enclosure!
Переглядів 1,8 тис.4 місяці тому
After some delay waiting for part we finally get started on the enclosure to house all the knee left electronics. If you want to see how I got to this point in the build check out this link to the playlist: ua-cam.com/video/NiXFlVzR29Y/v-deo.html And for the CNC machine build (short version) check out this playlist: ua-cam.com/play/PLBhXglGlotqwcu7XSOL7SebFkrHVn7Plx.html All music is free to us...
Deluxe Heated Threaded Insert Press | 3D printing
Переглядів 1,9 тис.4 місяці тому
After my first attempt at pressing in a threaded insert did not go so well I decided to make a press tool. I had a look around the internet at various designs and settled on one with the most interesting features. Let's hope it works!
Ep50: Drill Press upgrade | Time for some lights!
Переглядів 1,5 тис.5 місяців тому
The original light I installed behind the quill worked out but it could have been a bit brighter. So here we go installing some upgraded units. Very pleased with it now! If you want to see how I got to this point in the build check out this link to the playlist: ua-cam.com/video/NiXFlVzR29Y/v-deo.html And for the CNC machine build (short version) check out this playlist: ua-cam.com/play/PLBhXgl...
Never 3D printed anything! My new Bambu Lab P1S !
Переглядів 1,6 тис.5 місяців тому
I've seen 3D printers on UA-cam and a few in real life but never owned or operated one! Luckily I do have some 3D modelling CAD / CAM experience so hopefully that will help. Here is a short video showing my experiences with the Bambu Lab P1S, from unboxing to getting a print out! Here we go . . .
Ep49: Drill Press upgrade | finally getting the knee DRO fitted !
Переглядів 1,5 тис.6 місяців тому
Time to get the knee (Z) read head installed so we can readout the knee position on the DRO unit. A few bumps along the way but we got there! If you want to see how I got to this point in the build check out this link to the playlist: ua-cam.com/video/NiXFlVzR29Y/v-deo.html And for the CNC machine build (short version) check out this playlist: ua-cam.com/play/PLBhXglGlotqwcu7XSOL7SebFkrHVn7Plx....
Ep48: Drill Press upgrade | Adding a brake to the knee!
Переглядів 2,2 тис.6 місяців тому
We sorted out the back-drive problem, now the knee won't stay in place when drilling - gimme a brake! If you want to see how I got to this point in the build check out this link to the playlist: ua-cam.com/video/NiXFlVzR29Y/v-deo.html And for the CNC machine build (short version) check out this playlist: ua-cam.com/play/PLBhXglGlotqwcu7XSOL7SebFkrHVn7Plx.html All music is free to use from the U...
Ep47: Drill Press upgrade | Can we fix the backdrive issue?
Переглядів 2,4 тис.7 місяців тому
The knee is moving but now we have another problem - ballscrew backdrive! Can this gas strut help? If you want to see how I got to this point in the build check out this link to the playlist: ua-cam.com/video/NiXFlVzR29Y/v-deo.html And for the CNC machine build (short version) check out this playlist: ua-cam.com/play/PLBhXglGlotqwcu7XSOL7SebFkrHVn7Plx.html All music is free to use from the UA-c...
Ep46: Drill Press upgrade | Can we finally get this thing moving?!
Переглядів 3,2 тис.7 місяців тому
I track down the cause of the motor stalling and finally get this thing moving! If you want to see how I got to this point in the build check out this link to the playlist: ua-cam.com/video/NiXFlVzR29Y/v-deo.html And for the CNC machine build (short version) check out this playlist: ua-cam.com/play/PLBhXglGlotqwcu7XSOL7SebFkrHVn7Plx.html All music is free to use from the UA-cam audio library fo...
Ep45: Drill Press upgrade | Let's rebuild it!
Переглядів 3,4 тис.7 місяців тому
In this episode we re-build the drill press and test out the new stepper motor system. Hope it works . . .! If you want to see how I got to this point in the build check out this link to the playlist: ua-cam.com/video/NiXFlVzR29Y/v-deo.html All music is free to use from the UA-cam audio library for creators
Ep44: Drill Press upgrade | Tear down time !
Переглядів 2,6 тис.8 місяців тому
Ep44: Drill Press upgrade | Tear down time !
Ep43: Drill Press upgrade | More Power !
Переглядів 1,7 тис.8 місяців тому
Ep43: Drill Press upgrade | More Power !
Ep42: Drill Press upgrade | Lift Motor Problem
Переглядів 2,7 тис.8 місяців тому
Ep42: Drill Press upgrade | Lift Motor Problem
Ep41: Drill Press upgrade | Starting the knee lift electronics
Переглядів 2 тис.8 місяців тому
Ep41: Drill Press upgrade | Starting the knee lift electronics
Ep40: Drill Press upgrade | Making it bigger . . .
Переглядів 1,8 тис.9 місяців тому
Ep40: Drill Press upgrade | Making it bigger . . .
Ep04 DC solar monitor - Upgrade to closed loop!
Переглядів 42610 місяців тому
Ep04 DC solar monitor - Upgrade to closed loop!
Ep03 DC solar monitor - it's working!
Переглядів 35610 місяців тому
Ep03 DC solar monitor - it's working!
Ep02 DC solar monitor - proof of concept
Переглядів 44910 місяців тому
Ep02 DC solar monitor - proof of concept
Ep01 DC solar monitor - where to start?!
Переглядів 55510 місяців тому
Ep01 DC solar monitor - where to start?!
Ep04: Going Solar with UPS Solar | Finishing the installation!
Переглядів 555Рік тому
Ep04: Going Solar with UPS Solar | Finishing the installation!
Ep03: Going Solar with UPS Solar | Starting the installation!
Переглядів 530Рік тому
Ep03: Going Solar with UPS Solar | Starting the installation!
Ep02: Going Solar with UPS Solar | Custom Shelving!
Переглядів 742Рік тому
Ep02: Going Solar with UPS Solar | Custom Shelving!
Ep01: Going Solar with UPS Solar | Custom cooling!
Переглядів 928Рік тому
Ep01: Going Solar with UPS Solar | Custom cooling!
LINN tools tailstock DRO review - any good ?
Переглядів 2,7 тис.Рік тому
LINN tools tailstock DRO review - any good ?
Ep10: Clough42 Electronic Leadscrew | It works (eventually)!
Переглядів 10 тис.Рік тому
Ep10: Clough42 Electronic Leadscrew | It works (eventually)!
Hey friend, your video content left a deep impression on me. Is it possible for us to collaborate on a project at some point? Let me know your thoughts and keep working hard!
Hi. Thanks for your interest. Are you from the Bestarc company? I'll be spending the next 3 to 4 months of my spare time making this CNC plasma machine so that will be my main project for now. I have looked at your website and it looks like you only sell plasma machines and MIG welders. I have just bought your plasma machine, and I already have an expensive MIG welder, what sort of project were you thinking about? Maybe I'll email your customer services with a link to this video and we can continue this over email, thanks.
Great video! I'll have to check out one of those cutters, it seems way better than the old CUT50 I have. I hope you don't mind if offer some completely unsolicited feedback/thoughts. Have you calculated the amount of flex you are going to see when the torch is all the way out on the cantilever? I know you're going to have a THC and that will take up for some of that. If you want to stay with the cantilever design, I think you might have to upsize the gantry beam. I'd also consider rotating the beam 90 degrees. You'll have more rigidity with the larger side vertical, more metal resisting that moment. You might also consider placing your rails on adjacent sides of your gantry. Say, move the one on the top furthest from the screw to the front face of the beam. Then you can move the screw to the top of the gantry more centrally located to the center of mass of the x carriage. Possibly the same thing on the X. I'm a tad worried about the twist with the rails that close together.
Thanks for that. I did ask for thoughts and advice so it is all welcome. If you look at the CAD again there is a vertical 40x80 section joined under the top 80x40 section to form a very deep L shape. So it is much deeper than 40x80 alone, more like 80x120. I also wanted to keep the mechanical parts, especially the ballscrew out of the way of the plasma so put it on the back. I did look at the Langmuir and JD garage cantilever designs. I think I have much more section than theirs and the 20mm linear rails and carriages are very stiff compared to 3D printed bearing holders used on JD garage. Gantry beam is aluminium and Y&Z axis will have weight reduction where possible (holes, 3D printed parts etc.). When it is built I'll test the deflection and maybe measure the stiffness at the end of the gantry. I'm OK with it, especially with the THC but let's see!
@@routercnc9517 Right on! I figured you must have thought about this stuff in your design. I'm looking forward to seeing the build and the tests!
85 pounds for that extension? You've been had!
Probably! But it was one of those industrial places with a counter, I needed the parts to confirm it was all working and there was a queue starting behind me. The Rectus fitting feels nice and quality and there are a few adapters put together, and I needed an extension on the airline so went for it. Was hoping to pay <£50 but here we are.
You really, really should not use ball-screws on a plasma. Do check my other channel, i have built and retrofitted over 30 of cnc plasma machines by now. Chanel name is toma . cnc
Looks like my comment was deleted...
I had another person’s comment arrive in my email but it was gone in the UA-cam comments. So I couldn’t reply which makes it look like I am ignoring them. Try replying to this one.
@@routercnc9517 Yes, I know YT delete some comments. My yesterday's comment contained 3 links, so, maybe was that, no idea. Was only to tell you the 3 videos the "Cracktown City" guy did about his CNC plasma cutter. Not the same style, but have some good ideas. I suppose you already saw them, but just in case. I'm gonna write again the 3 links in my next comment, right below this one, we'll see what happen
ua-cam.com/video/T-vQkJGF1Ts/v-deo.html ua-cam.com/video/ggnd5RdA-Yo/v-deo.html ua-cam.com/video/BBJ6rFitng0/v-deo.html
@@routercnc9517 Yep ! Links deleted !
@@routercnc9517 My comment with the links was deleted and also my next comment telling you was deleted, no links this time... Not sure this one will be deleted, too...
I love a new project looking forward to this one
Me too!
Might be worth a look into the MyPlasm controller (by Proma) it comes with a dedicated THC interface controller. It is purpose built for cnc plasma setups...
I think I looked at that and it was quite expensive. I'll have another look to see what it offers and compare to my current direction. Thanks.
In the US, 1 litre office PCs, such as the Dell Optiplex Micro line, or the Lenovo Tiny machines are dirt cheap used 3-5 years after they came out. Maybe the market isnt this way where you are, but here such a used office machine will be way cheaper than just about any NUC.
I've not looked at those so I'll check them out. I quite like the idea of the PC being inside the control cabinet and out of the way so the NUC is a nice option and there are some models around £100. I'll see how they compare for size and availability, thanks.
The amount of money for all the materials and machining time with build would still run you a good weeks of work and cost almost as much as a mini mill would..
Used many NUCs from iCubes on small Automation Machines at my last place - really really good
OK thanks. I'll look at those. The ones I had a quick scan over where some Banggood units around £90. Came with HDMI, USB, WiFi, network, and Win 11. I'll see if Banggood would be interested in a review!
OK, look nice but no prices on the iCubes website (for some reason could not find Automation Machines but could be me!). "Look" more expensive than my cheapy option, although those are new ones, probably don't need much performance as controller should do the work.
yeh........ New Build, great.
thats interessting that the US model has an US air connector but an EU plug. very Strange
I think it is because I emailed them and said I was based in the UK. For the US model they would normally include an adapter to take the EU plug into a US plug, but they left that out of the box for me. The price point / features meant I was happy to make it all work.
Have you thought about the dry air requirements. Looking forward for the build. I have built a 4x3 plasma with water table
The manual says the built-in one is OK for low volume DIY, but above that then consider another air filter. When I was in the industrial pneumatic shop the other day I did glance at the filter kits, but didn't ask about prices! I think the trade off is less life on the consumables. I did think about a water tray but didn't fancy the mess. I'll try the downdraft funnel type into a bucket, with a fan just above the bucket blowing the smoke out of the garage door and see how it goes. I'm leaving the design open so I could retro fit a water tray if that ends up being the better option.
What did you go for on the air drier? I’ve seen people use the type with absorbent granules inside which change colour.
that is not a relay, it's a solenoid valve, it has to be connected to a relay inside the control box
I received mine last week, and from watching your video, they have changed them slightly regarding the automatic pressure cut off on top of the tank. Mine has 2 of those small black boxes on top.
OK that’s good to know. Hopefully still works the same.
Never been a fan of misting in a small environment. Air quality for my lungs is quite important to me...
Agreed and the idea of that was to not create a mist. It is similar to the fogbuster in principle but I find it a bit fiddly to set each time to get it mist free.
Hi there, I just thought I would weigh in with unsolicited advice as usual :) The only thing that really matters with an air compressor is how much volume it can provide at the working pressure. The storage capacity of the tank really only serves to introduce some duty cycle for the motor, but usually this can be improved with better cooling. If you would really like to test the performance of the compressor buy a small needle valve that fits on the end of your air hose, turn the compressor on until it is full then use the needle valve to let air out until the compressor starts, take note at what pressure the compressor starts at, set the needle valve to let out as much air as the compressor is supplying so that the pressure stays constant, say 90 PSI inside the tank whilst the motor is running. Use the water displacement method to measure the amount of air coming out of the needle valve, you can take this measurement every minute for say 10 minutes, also measuring the temperature of the compressor body at the same time until the compressor reaches a temperature that you feel you need to stop the test. Compressors like this are often oilless and rely on a oring to seal the piston to the cylinder, or sometimes a fibre washer, cooling is really important and is really the major limiting factor to their use, after a while the compressor gets too hot, the air it is compressing is hot also so needs compressing further and the whole system becomes less efficient. Anyway, my two cents worth!
Always good to have your unsolicited advice Matt! I did consider running something more like that test and bought the anemometer to also add some measure of flow rate but decided I'd just go for how long you can run a tool for. I like your ideas though as it goes much further than my original plan. One thing I wondered was how fair it was because the hose attached to the compressor which went to the valve (for finding the balance point of pressure as you describe) would have a certain inner diameter which would also be a variable. Although I could make sure the pipe was larger than anything on the compressor. I have noticed the motor does get hot with prolonged running, not worryingly so but it does heat up. Anyway I like your thinking because flow rate at a given pressure is probably useful to match to the tool you want to use. I think this is because the max pressure spec is typically the max pressure at low/zero flow and the max flow spec is most likely at very low pressure. In other words 2 ends of the performance curve which are not that helpful since real use is in the middle of that plot. I'll think about something flow related, maybe one video for the future sometime, who knows!
@@routercnc9517 Thanks for your reply, the thing to remember is that when the motor is running and the tank is not at pressure, essentially the motor is free spooling only having to overcome the internal friction of the drivetrain and moving the pistons etc. Only once the pressure builds up does the motor actually get loaded and have to produce any meaningful torque. It would be like testing the performance of your car by revving it in neutral, it is a pointless test that doesn't reveal anything. You can use compressor fill time calculators to get close to a representation of output, but in my opinion that isn't really relevant, when you are using air tools, especially like ones that use pneumatic motors, your compressor is going to be running pretty much all the time and you need to be able to maintain it at working pressure. And for the motor with the temperature increase, the resistance increases also, which reduces the power and torque of the motor, this along with having to compress hot air makes a surprising difference to efficiency. With my compressor in my home shop, I have 6 small compressors that are controlled with an arduino, they measure the rate of decrease of the air pressure and using something similar to a PID loop it switches on more compressors to compensate, there is also temperature sensors on the compressor bodies so the hottest compressor is rested, and the code makes sure they all get a similar amount of run time, was a great project, learned a lot! Pretty interesting subject really. Thanks for your videos, always enjoy them!
That’s an unusual setup- sounds like someone needs to start their own channel!
@@routercnc9517 Too camera shy!
I wanted to buy a silent one after moving to a different place, but it struggling with the belt sander made me reconsider. Might have to save up to buy a screw compressor 😅
Yes, it won’t run a sander so time to save up a bit more.
my friend, there was a different guy that i saw on youtube who built an acoustically isolated exterior equipment cupboard outside of his garden shed. purely to house the air compresser and that made is completely silent for everybody. that was a great solution... but then there was also another guy which i saw here on the youtubes. who didnt do that. but what he did was to very simply daisy chain 1 extra very large tank onto his pretty ordinairy "too small volume" regular compressor (like yours). very simply to not have to buy some large compressor. just with some few extra valves and regulator or something relatively simple. so there's another one to think about too (in combination), if it was not worth doing the exterior equipment cabinet purely on its own merely for only 50 litre sized compressor. however i myself am not so sure how it compares to simply just buying a brand new larger compressor. since with a larger one it might be more powerful to recharge faster and so on.
I think I saw some examples like that. Wouldn’t work for me as outside the workshop wall is the neighbour’s wall so it would be annoying for them.
I bought that compressor, partly based off your previous video. My previous one was second hand, smaller, older and much more noisy. My uses were very similar to yours (air for cleaning chips and a CNC mist system), but I've added in some popes to distribute the air around the garage, and I got a small sand blasting cabinet. If someone wants to use it for sand blasting, it's ok for occasional use, but you have to stop quite often. I plumbed in the old compressor as a remote tank, and that helps, but if you were doing a lot of it, something with higher output and/or a bigger tank would probably be the way to go. One question I had about the CNC mist system, I tried WD40 but I found it caused the chips to clump up. I switched to Isopropyl Alcohol, which seems pretty good so far, but I have to keep the garage well ventilated... Have you tried it?
I’ve thought about IPA but never got round to trying it.
I think you should just get it over with and turn this into a cnc mill! There plenty of DIY mills on UA-cam for inspiration.
Tempting but a fair bit of work in quill/spindle. Also the knee is only supported on 2 linear carriages so not very stiff for lateral forces.
Hi, nice one getting this all to work. I'm quite interested in the Harvi interaction part. I'm just about able follow what you're doing at 14:00 Would you be open to sharing the PCB schematic at all / at least for that side?
Ah nvm, I think I get it now. If you had a 9V ac/ac adaptor it would essentially be an LDR in series from the adaptor going to the Harvi I think. Suppose it’s possible the resistor divider is also helping in some other way - sounded like it was very sensitive to alterations here.
Essentially yes. The resistor divider was needed to drop the AC voltage to a level the Harvi needed. They were 1 Watt because they needed to allow enough current to flow as that is what the Harvi needs to sense. They get warm but not hot.
I couldn’t find an AC /AC adapter which output a low enough voltage. Otherwise they would not be required.
@@routercnc9517 Thank you for the elaboration, I’ll do some experimentation!
Yes Sir watching a rerun better than cable.
OK, happy viewing!
What software version are you running?
Do you mean on the CNC machine? That motion control software is called UCCNC. I installed in around 2021 and the manual shows it to be software version: 1.2111. If you mean the software version for the microprocessor code uploader (Visual Studio??) into the TI board as part of this ELS project I used the exact same version James showed in one of his videos. I tried the current version at the time when I built mine and I could not get it to work. So I re-watched his videos and downloaded a the same legacy version as James and that worked fine. Of course because he made this a few years earlier that was the latest version for him a the time. It was too long ago and I can't remember the exact version but watch his videos and you will see it when he installs the code developer software and hooks it up to the microprocessor. If you meant something else, please let me know.
@@routercnc9517 I meant the Clough42 ELS. I wonder if my issue is the same as yours. I will try the earlier release. Did you report the issue?
Ok, ELS version 1.4. The other issue was with Microsoft Visual Studio and no I did not report it to Microsoft
@@routercnc9517 Thanks for the info. Troubleshooting is always a process of elimination.
For the backlash, you can just put 0.1mm variable compenastion in driving that motor
Ooh! Yes that’s a great idea. Software backlash compensation on change of direction.thanks!
Looks like a cnc mill now :) For the thrust bearings, I hope you didn't forget to grease them (I think the video just shows the dry fitting).
Yes they had a light coat of grease. Not much as they would attract dirt and maybe swarf.
Glad u sorted that out still think u should mill with it lol
Don't encourage that other guy!
In my opinion you are one of the best narrators on UA-cam.
Thank you, that is very kind of you. I'll just keep on doing what I'm doing!
Thanks for the content! I just want to see you build stuff.
OK thanks. I’ll see what I can do!
its just a simple drill 🙂 nice work again.
It certainly used to be!
One advice about the ferrules.. Strip the wire long enough to just protrude the bottom-end.. This way you always have the optimal conductivity (...And don't twist the wire together when using ferrules)
Thanks. I've used lots of ferrules since this project was uploaded and tend to do that now.
I want to try a similar technique for 3d printing + laser router application, so not realy care about possible polymer creep under load. My surfaces are in a square of 500x500mm. Only thing around i could think about is a sizable thick glass slab with thin selfglued grinding paper. Getting a mill guy or real precision tools bloats budget roughly ~50%, so i try to avoid it for now. Would be glad to hear any tips.
If you mean tips for epoxy for self-leveling, then try not to mix any air bubbles in. One way is to mix it in one jug, then open a hole near the bottom and let it flow carefully into another jug. Then pour from the second jug onto the frame. This is to minimise air bubbles because these will upset the final surface. Or invest in a vacuum chamber to release the bubbles that way.
How did it work in your case long term?
Many years later and no issues at all
Very nice work. Interesting. Gave me good ideas on my drill press
OK, go for it!
Darwin would love this machine, so much evolution going on 😄
Yes, very little left of the original drill - just how I like it!
Quick question, how did you select your printer, specially the P1S vs X1C. I know there is a cost differnece btween, but do you think the X1C would have offered more value now you have used the printer. I only ask as my printer has recently gone faulty, and im between do i repair or make a resonable upgrade into Bambu. Great channel, great content
I looked into a range of printers while researching and the new Bambu Lab printers seemed to be at the next level according to reviews. So then it was looking through the range - A1 mini, A1, P1P, P1S, or X1C. Mini was a bit small (180x180?), P1P was same as the P1S but w/o enclosure, and X1C had the same basic mechanics as the X1C but was considerably more expensive. I think the X1C with AMS was getting close to £2k, whereas the P1S with AMS was £900. When I asked my colleagues they said what do you want to do with it? Well as a beginner that is a difficult question because you don't know what is on offer and what could be done. So that's why in the end I went with the P1S because it was enclosed, so could print more materials, had a good size print area, had the AMS to allow multi colour prints (do I need that!?, yes is the answer it turns out) and I could buy this model plus lots of filament as still be much cheaper than X1C with AMS. I think the X1C had a few more sensors, and had hardened nozzles etc. but I think the P1S could be upgraded for not much money to have some of those parts. So on reflection I have no regrets on this model. It seems to do so much for you, prepping the nozzle, cleaning it, purging, auto bed levelling, that for the most part you can send a print and walk away. You can monitor progress on your phone app, and you get a message when it is done. The only times it has lost adhesion was when the part was getting quite large (fixed with adding a brim, and +5 deg on the bed), or the part was almost up to the edge of the build plate because it was a big part (fixed by printing 2 small pieces and clipping them together). It is also very fast. It is my first ever 3D printer so you will need to research a bit but I would buy it again without hesitation. I've even considered the A1/mini as a cheaper side kick to speed up iteration of parts, but I think I'll not get that past finance!
I think you are spot on with all those comments. For anyone that's interest Bambulab are having a sale until the 5 July. The p1s with the ams is 140£ off usual list
Hi - use the tone function in the arduino software, rather than hard coding each pulse event into the software - You then won't run out of clock cycles on the arduino as the tone function operates outside of the regular code execution speed. You can calculate tone to RPM or to mm/s by working out the steps per revolution and ball nut pitch etc. That is the best way I have found to control the rotational speed of a stepper motor (rather than the more normal position type control). I would also code in a deceleration as well, at higher speeds and hard stops it might miss a step or two - might not matter too much, but if you are trying to keep track of position based on step counts, then that might catch you out.
Hi Lewis, OK sounds good. I've had lots of suggestions over using different libraries for stepper control and there are quite a few. I did wonder if they take up more clock cycles to branch over to and in the end because I enjoy tinkering I hard coded the pulses, so good to know they run separately. As you can see it runs plenty fast enough though and I'll probably stick with it as it is working. But for future projects I'll look into the tone function. I wondered about the deceleration so I guess it could loose steps. On a CNC machine that would be a problem but maybe not too big a deal here as when running high speed you are probably just getting somewhere near you need to be. The knee DRO can track where you are in absolute terms. It might be a bit more sympathetic to the mechanicals though and stop the grub screw coming loose. I think 3 lines of code should do it . . . ?
@@routercnc9517 yeah a ramp down will definitely be more mechanically sensitive. Not sure how you are running your ramp up at the moment, but my solution was to use a while loop. While currentTone<targetTone; currentTone++, tone(currentTone, stepperPin);. Don't quote me in that, but it's close enough to give you the jist. In that case targetTone is the rpm to want converted to Hz, at the start currebtTone is zero, and then as the whole loop runs, the currentTone valuenisnincreaded.by one each time until it reaches the desired value. If that ramp is too slow, you can either increase by two or three or four each time, or divide the target tone by a set vale and use that, which then gives you a ramp over the same time period regardless of end speed i.e. the higher the target speed the more aggressive the ramp. Oh, the above is for ACC, just to the reverse for deceleration with the appropriate tweaks. The above code would also need to ensure that you are using interrupts for your inputs and once the ramp starts it won't stop until it has exited the while loop.
The interrupts fix that issue and are good practice anyway
Also, Arduino’s web based IDE I believe supports OTA (over-the-air) compiling on some of their boards. Using a ‘OEM’ OTA solution is surely the way to go, especially for firmware updates.
I've come so close to getting this to work with HC-06 bluetooth modules I may give it another go. These Nanos are so cheap if I can make it work I can cover many such projects. However, there are other boards with WiFi and other systems already set up for SOTA so that is an option too. I'll also look into web based IDE as you mention. I do seem to like doing things myself (I learn more that way, but it can take longer!). Here is the history so far - I have managed to set up a Nano to act as serial host to talk to the HC-06 and I can use AT commands to talk to it. I used different pins (10 and 11) to keep the TX and RX free otherwise it does not work. There was a library which allowed data to be transmitted on these other pins. I then set the Baud rate from the default of 9600 to 115200 which is supposed to be the max for the Arduino but it stopped talking after that (I matched the Baud rate in the sketch to this value so it should have still worked). So I bought another HC-06 and left the default Baud rate at 9600 (I guess this means slow uploads, but let's get it working!), got it talking via the Nano using AT commands. Then plugged in the bluetooth USB into the computer and got it linked to the HC-06. It showed up as COM6 on my PC, which was a good start. Then I had to reconnect the TX and RX wires (which had been on pin 10 & 11) between the HC-06 and the Nano as we were now supposed to be sending data from the PC to the HC-06 and into the Nano via these proper channels. But IDE could not recognise the COM port and would not upload a sketch. Note this is HC-06 which is only a slave unit (not HC-05 which can be master and slave) and only has 4 pins, Vcc/GND/Tx/Rx. Feels like one step away but I'll come back to it another time since the software is working OK for now.
New subscriber here. Really enjoying this project, not enough software controlled drill press videos out there on the tube. Any chance you’d be willing to share your code with us? Also, if you’d like to setup a Discord or something for this project to support people wanting to undertake something like this as well as to share ideas, I think that would be sweet.
Hi MakerMadness. Welcome to the channel. Have a look around - I tend to get involved in long term projects so be prepared! Yes, happy the share the code. I noticed when editing the video that some of the variables were not used in the end, plus add-ins such as the EEPROM support (to save values when powered down). Also be aware it is flat code, no function calls, and does not make use of the many stepper type libraries out there, I wrote that code myself. As for Discord I've heard of it but have never looked into it. I don't have much time for many of the social media sites (videos take long enough!) but I have been a long time member of the 'mycncuk' forum. I'll put a link in the text box above to the long thread on this build series. If you check it in a few days I should have uploaded the code there as a zipped file. I'll post in this reply when I've done it. Hope that works for you. Thanks.
@@routercnc9517 would love to take a look at the code, do you have a avenue in which you may share it with us?
Hi MakerMadness OK, I've uploaded to the code shown in this video to the mycncuk forum. See link in the text description box above. Or search for 'mycncuk metalworking pillar drill experiences' and scroll to post #105.
Hi, I've just discovered your channel and I'll be here watching videos for a while xD Someone on garage journal linked me here, they thought you might have some advice for me on buying a milli n New Zealand (I'm in christchurch) ... would you be willing/have some advice to share? I have about 12k NZD to spend, should I be looking for a used VMC, a new Machinery House mill, a used second hand mill in that price range, or anything I haven't thought of? Thank you!
I don’t own a milling machine. I have built my own CNC router though. Current project is a heavily modified drill press but it cannot be used for milling. You would get a good response from the mycncuk forum. Lots more mill and VMC users. Thanks
@@routercnc9517 thank you :)
@@ASW4567 If YT will let me put a link here the forum is here:www.mycncuk.com/index.php It can take a bit of time to get through the moderation and be able to post. If you get stuck give me a reply here and I'll nudge the site owner.
I doubt that you are fighting a surge. More likely all those coils opening and closing are creating radiated EMI. This tends to get recieved by cables in the box. The cheap and easy way to deal with that is by adding a ferrite bead as close to the source of the high frequency noise. EMI is traditionally contained by using a "star" grounding methodology to protective earth. (not Ground 0v). Having shielded cabling with the shield running to a single PE will prevent wiring from capturing radiated noise.
Thanks. I think shielded cable would have been my next step on more of the cabling if the capacitor had not worked (the stepper motor cable was already shielded to PE via the lower panel, but other cables were not). I do have some ferrites so I'll try those if it starts playing up in the future. For now the capacitor seems to be working.
Do you have a flyback diode across the brake solenoid? Without it, you will be dealing with inductive flyback voltage that can cause noise the issues you are seeing. I also recommend that you isolate the brake solenoid circuit is isolated from the electronics, if possible.
I think I showed it in the video but yes there was a diode across the solenoid/electromagnet - it was at the power supply terminals. Yes the 24VDC circuit just goes from the power supply, through the relay contacts, and to the electromagnet, so separate in terms of the wiring at least. Looks like the capacitor sorted it anyway, thanks.
Interference is a bugger to track down, but when you find it, it's all worth it, (but not when you find that you caused it in the first place, ask me how I know). Good job on finding it. I think I'd like it better if the controls were a bit closer to the front , rather than having to reach over to the back of the machine, but that's just me, I'm only short :), you made a nice job of it, I like it.
Thanks. It looks further on camera plus I was leaning out of the way to allow you to see the knee whilst I pressed the buttons. In practice it is fine for me to reach. Also saves me pressing it unintentionally and raising the knee into the workpiece.
Love the toys r us hammer, a bit of a technical one for me love the 3D printing
Yes I have a storage case dedicated to wall fixings. Has brown, red, yellow plugs, 5, 6, 7mm masonary bits, small hammer (big one does not fit), AC voltage detector (to check for cables in the wall). So if I need to fix something to a wall it's all in there.
@@routercnc9517I have something similar, everything ready in a compartmentalised box. However, I gave up using red plugs etc years ago. Now ONLY use various types of Fischer wall plugs. I know they can be 4 times the price, but I have never had the problems I used to get with those red and brown plugs. For the sake of a couple of pennies I know that I'm not going to be called back to a job because "Its come loose."
You must only be using a Class X capacitor across the main! Edit: sorry, when I saw the blue-and-brown cable...
Yes, poor choice of wires for debugging! Only 24VDC used here for the electromagnet, but good advice if I was using mains.
Choose the random seam position to lose that line in Bambustudio.
OK thanks, I guessed there was a way to sort that. I'll do that next time.
People that ask "but, why?" obviously have no clue.
I guess you could ask that about anything. Mountain walking, motor racing, horse riding. If it makes you happy then it's all good.
@@routercnc9517 lol! True story.
looks good 🙂
Thanks Pierre, good to see you still following along.
YOU KNOW you've no intention of not turning into a milling machine? You know you want to!😁😁😁
Still tempted. . .
The one big criticism I've got is that you tend to explain TOO much, things that you've already told us, or that is obvious even to a non engineering type like myself. Overall though I enjoy the blogs
Ok thanks for the feedback. The videos take a long time to edit so I probably miss how often I say something. I’ll watch out for that. Out of interest do you prefer just machining? Or just a quick intro and then jumping to finished parts? I’ve tended to edit as if you are following along and might do something similar. All feedback is welcome, thanks.